Key Steps and Processes in Casement Window Production Design
For window manufacturers, producing high-performance casement windows requires a meticulously designed manufacturing process. These windows undergo strictly controlled steps, integrating aesthetics, functionality, and durability—from material selection to final quality verification. Leading producers leverage advanced technologies to meet building code requirements while ensuring energy efficiency, security, and flexibility for custom designs.
Material Selection & Preparation
Metal Alloys & Thermal Optimization
Premium casement windows typically utilize aluminum or steel. Aluminum offers excellent corrosion resistance, making it ideal for coastal environments. Steel provides superior strength, enabling slimmer sightlines. To enhance thermal efficiency, manufacturers integrate polyamide thermal breaks. These breaks significantly reduce heat transfer. Fiberglass is another option, achieving R-values up to 7. Material choice directly impacts thermal insulation performance and structural longevity.
Glazing Specifications & Performance Ratings
Double- or triple-pane glazing is standard. Laminated glass enhances security and can reduce noise by up to 50 dB. Low-emissivity (low-e) coatings reflect infrared heat. Argon gas fills between panes minimize heat loss. For dynamic control, electrochromic glass is emerging, enabling on-demand tinting. These features help meet ENERGY STAR® certification standards.
Profile Processing & Machining
CNC-Driven Precision Cutting
Computer Numerical Control (CNC) systems machine raw materials, cutting aluminum or steel profiles to sub-millimeter accuracy. Automated saws handle complex angular cuts for arched or circular profiles, eliminating human error. Brands like KANOD utilize CNC technology to ensure consistency, with every component matching the digital design perfectly.
Joining & Welding Techniques
V-grooving prepares corners for assembly. Precision welding fuses joints, with robotic arms ensuring uniform seams to maintain structural integrity. Specialized welding techniques for steel windows prevent distortion, preserving clean lines. Each weld undergoes quality inspection to verify alignment and strength.
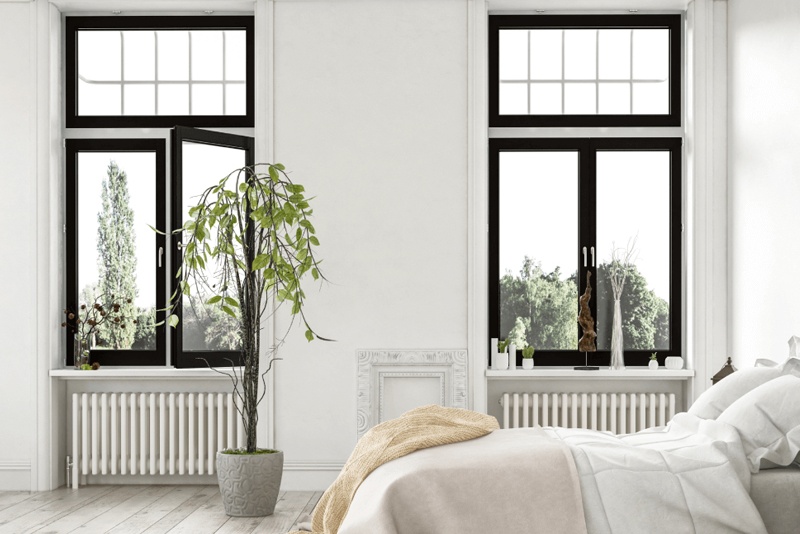
The bedroom has a casement window
Glazing & Insulation
Insulated Glass Unit (IGU) Assembly
IGU assembly requires precise sealing, primarily employing two methods:
- Aluminum spacers: Faster production, stable seal, higher cost.
- Warm-edge composite rubber spacers: Slower thermal-bonded process; risk of condensation if defective.
Automated lines apply desiccants to absorb moisture. A primary seal of butyl forms the main barrier, while a secondary silicone seal enhances durability.
Tempering & Lamination
Tempering ovens heat glass to 620°C followed by rapid cooling, increasing strength by 5x. Lamination bonds glass layers with a polyvinyl butyral (PVB) interlayer, holding shattered glass in place. CNC glass cutting tables handle custom shapes, optimizing material utilization.
Hardware Integration & Assembly
Hinges & Locking Mechanisms
High-load hinges support sashes weighing up to 300 kg. Multi-point locking systems provide adjustable ventilation. Screw-and-gear mechanisms allow sash positioning at any angle. Manufacturers often integrate globally recognized hardware brands.
Weather Sealing & Gasket Application
EPDM rubber gaskets are critical for blocking water and wind int
rusion. Extruders form continuous gaskets, with corner vulcanization preventing leaks. Compression tests ensure seal integrity.
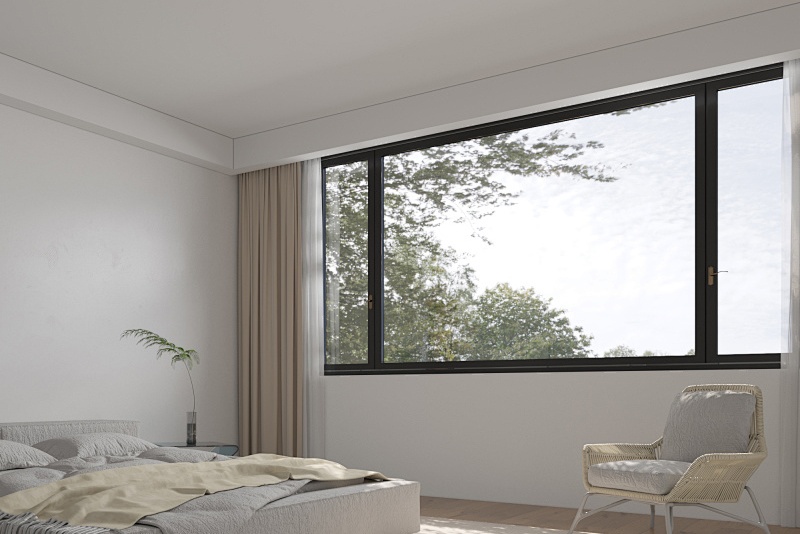
The bedroom has a casement window
Surface Treatment & Finishing
Automated Powder Coating
This 3-stage process involves:
- Chemical pretreatment: Degreasing and adhesion promotion.
- Electrostatic application: Uniform coating deposition.
- Curing: Heating to form a resilient finish.
Advanced lines reclaim up to 95% of overspray, minimizing waste. Finishes include matte or metallic effects; self-healing variants repair minor scratches.
Anodizing & Alternative Finishes
Anodizing thickens aluminum’s oxide layer, boosting corrosion resistance. Fluoropolymer coatings (e.g., PVDF) offer superior UV resistance for high-sunlight regions. Precise color matching is achieved using RAL color standards.
Quality Control & Testing
Performance Verification Protocols
Every window undergoes rigorous testing:
- Air/Water Penetration Tests: Simulate storms up to 150 mph.
- Cycle Testing: Hinges endure 20,000+ open/close operations.
- Thermal Imaging: Detects insulation gaps.
Tolerance & Alignment Checks
Laser scanners verify dimensional accuracy, ensuring gaps < 0.5 mm. Flatness gauges detect deviations, guaranteeing smooth operation.
KANOD: Benchmark in Advanced Manufacturing
KANOD exemplifies excellence in casement window production. Its CNC machines perform drilling and forming in a single setup, enabling complex geometries. Powder coating incorporates eco-friendly, chromium-free electrophoretic primers. Windows feature traceable digital IDs. KANOD complies with Passive House standards, and its lean workflow reduces lead times by 30%.
The Future of Casement Window Manufacturing
Smart technologies are reshaping the industry, with sensors monitoring air quality and self-tinting glass adapting to sunlight. Sustainability drives further innovation. For B2B clients, partnering with innovators ensures access to these advancements, accelerating project delivery.